Fascination About Lean Manufacturings
Wiki Article
A Biased View of Plastic Manufacturing
Table of ContentsThe Best Strategy To Use For Lean ProductionExcitement About Lean ManufacturingThe Only Guide for MfgManufacturing Industries for DummiesLean Manufacturing Fundamentals Explained8 Simple Techniques For Additive Manufacturing
The text on this page is an example from our complete White Paper 'Shot Moulding for Purchasers' - * Example message * - for complete overview click the download button above! Introduction This guide is intended for individuals that are aiming to source plastic mouldings. It gives a much required insight into all that is included with producing plastic parts, from the mould device called for to the moulding process itself.If you wish to explore additionally, the overview covers types of mould tools, along with special ending up processes such as colours & plating. Words that are underscored can be found in the glossary in the appendix ... Component I: Moulding: The Fundamentals The Advantages of Injection Moulding Plastic shot moulding is a really accurate process that provides a number of advantages over other plastic handling methods.
Accuracy is excellent for really elaborate parts. You can hold this moulding in the palm of your hand and also it has employers, ribs, steel inserts, side cores and also holes, made with a sliding shut off feature in the mould device.
Manufacturing Industries Things To Know Before You Buy
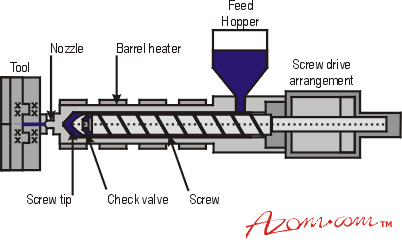

from product feed & melting; product shot; cooling time and ejection to the re-closing of the mould device ready for the next cycle. Draft angles - The wall surfaces of a moulded part must be a little tapered in the direction in which the component is ejected from the mould tool, to allow the part to be ejected quickly.
Ejector stroke - The pushing out of ejector pins to expel the moulded part from the mould tool. Ejector stroke speed, size and timing needs to be carefully controlled to protect against damage to the ejectors and also mould device, yet at the exact same time make the moulding cycle as brief as feasible.

Top Guidelines Of Die Casting
Ribs - When a plastic component has thin wall surfaces, ribs are contributed to the design to make the thin walls stronger Side cores - Side action which produces an attribute on a moulded component, her response at an opposing angle to the typical opening direction of the mould device. plastic manufacturing. The side core requires to be able to pull back as the plastic part can not be expelled or else.
Walls - The sides of a moulded part The message on this web page is a sample from our full White Paper 'Injection Moulding for Purchasers'.
Injection moulding is extensively made use of for making a range of parts, from the tiniest components to whole body panels of autos. Developments in 3D printing innovation, using photopolymers that do not melt throughout the injection moulding of some lower-temperature thermoplastics, can be made use of for some easy shot moulds. Shot moulding uses a special-purpose equipment that has three components: the shot system, the mould and also the clamp.
Mfg Fundamentals Explained
, with the quantity utilized of the previous being significantly higher.: 13 Thermoplastics are prevalent due to features that make them extremely suitable for shot moulding, such he said as simplicity of recycling, versatility for a vast range of applications,: 89 and capacity to soften as well as flow on home heating.In several cavity moulds, each tooth cavity can be identical and also develop the same components or can be distinct and also develop numerous different geometries throughout a single cycle. Moulds are generally made from device steels, but stainless-steels and aluminium moulds appropriate for specific applications. Aluminium moulds are normally ill-suited for high quantity manufacturing or components with narrow dimensional tolerances, as they have substandard mechanical properties as well as are extra prone to put on, damage, and also deformation throughout the shot and clamping cycles; nevertheless, aluminium moulds are cost-effective in low-volume applications, as mould construction costs as well as time are substantially decreased.
When enough material has gathered, the material is forced at high pressure and velocity into the part forming tooth cavity. The precise amount of shrinking is a function of the material being used, and can be relatively predictable. To stop spikes in pressure, the process normally uses a transfer position representing a 9598% complete tooth cavity where the screw changes from a continuous speed to a continuous pressure control.
The Basic Principles Of Manufacturing Industries
As soon as the screw reaches the transfer placement the packing pressure is used, which completes mould dental filling and compensates for thermal contraction, which is rather high for thermoplastics relative to lots of various other materials. The packaging stress is applied up until the gateway (dental caries entrance) solidifies. Because of its tiny size, the entrance is generally the top place to strengthen via its entire thickness.: 16 Once the entrance strengthens, say goodbye to product can enter the tooth cavity; accordingly, the screw reciprocates as well as gets material for the next cycle while the material within the mould cools to ensure that it can be expelled and also be dimensionally stable.Report this wiki page